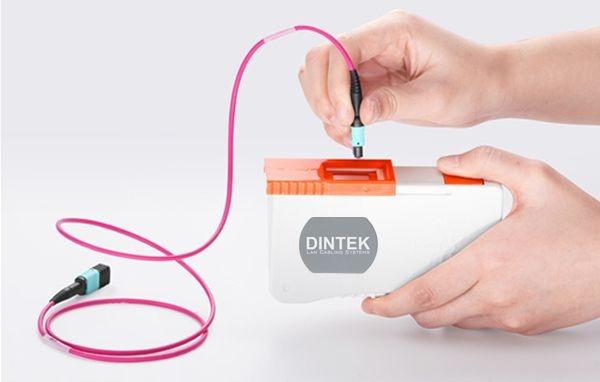
Why it's important to clean your fiber optic equipment
According to the textbook by Bill Woodward, titled Cabling: The Complete Guide to Copper and Fiber-Optic Networking, dirty fiber end-faces account for 85 percent of attenuation loss issues. To illustrate this, it can be compared to a typical human hair which is between 50 and 75 micron. A dust particle can be as little as 9 micron and is pretty much impossible to see without a microscope.
Despite this, it could completely block a single-mode fiber core, and if trapped between two fiber faces it can even scratch the glass, damaging the end-face. If this happens, then at best it will require the careful and time-consuming process of being polished out and, at worst, it will have to be replaced.
The cleaning process
Connector polishing
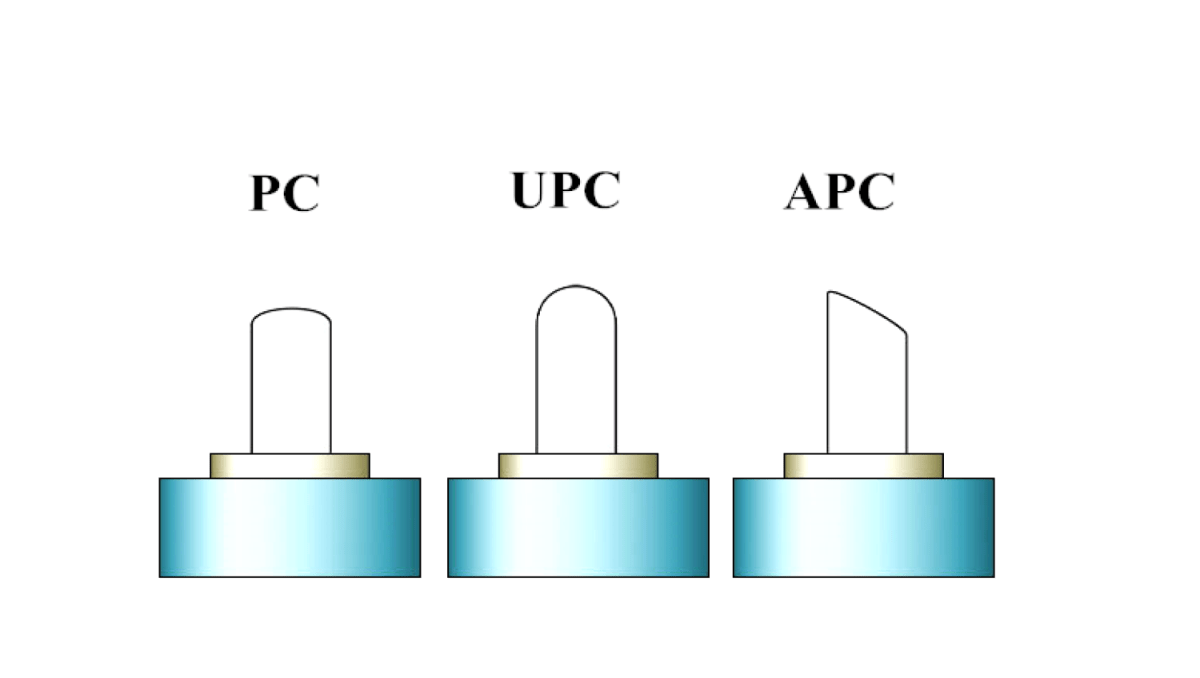
1) shaping the end tip until the desired shape is accomplished;
2) smoothening the shape to minimize light refraction.
Common polish topologies include physical contact (PC); ultra physical contact (UPC) and angled physical contact (APC). PC connector end faces are polished with a slight curvature. That convex shape locates the fibers at the highest point of the surface, which reduces air gaps between them. Typical return loss in these connectors in single-mode applications is -40 dB. An extended polishing is given to the UPC connector end face, which results in a better surface finish. The curvature makes them look dome-shaped. Their optical return loss is about -50 dB or higher. An APC ferrule is polished with an 8-degree angle that brings the fibers tighter and reflects light at an angle into the cladding instead of reflecting directly to the light sources, which causes its Optical Return Loss to be -60dB or higher, being the better performance connector.
DINTEK have a comprehensive range of fiber optic cleaning products each individually designed to clean specific connector types.
The range includes:
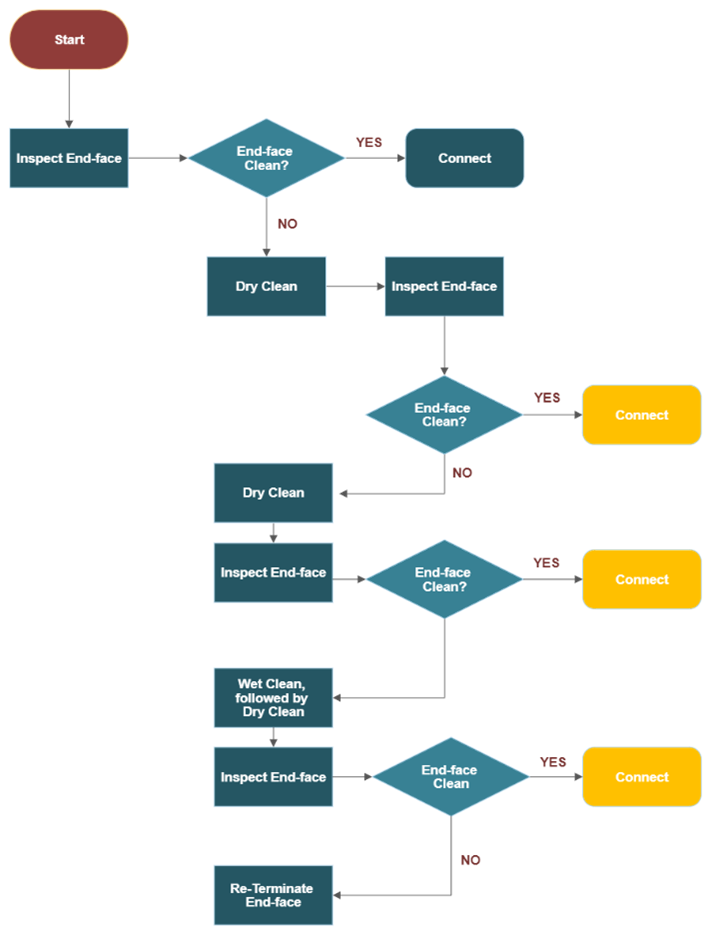
The do's and don'ts of cleaning fiber
- Never touch the end-face of the fiber connectors - natural body oil can be a major cause of contamination.
- Always keep a protective cap on unplugged fiber connectors - protection from both damage and contamination.
- Do not clean bulkhead connectors without a way of inspecting them - how else will you know whether the cleaning is successful?
- Always store unused protective caps in a sealed container - they can be a major source of contamination if not stored in a clean environment.
- Never touch the end-face of the fiber connectors - natural body oil can be a major cause of contamination.
- Always keep a protective cap on unplugged fiber connectors - protection from both damage and contamination.
- Do not clean bulkhead connectors without a way of inspecting them - how else will you know whether the cleaning is successful?
- Always store unused protective caps in a sealed container - they can be a major source of contamination if not stored in a clean environment.